Manufacturers of high-performance metal components—such as cutting edges, wear parts, and various fabrications—face unique challenges in quality assurance and production efficiency. For parts requiring heat treatment or precise geometries, ensuring every product meets stringent standards is essential. LM3 Technologies’ PAQi platform provides robust, AI-powered inspection, measurement, and automated handling solutions that optimize quality control, improve productivity, and reduce operational costs—all without the burden of recurring subscription fees common in the industry.
Advanced Inspection for Metal Parts
AI-powered inspection brings a new level of precision to quality control processes. In the manufacturing of cutting edges and wear parts, where flaws like surface defects, inclusions, or structural inconsistencies can compromise performance, reliable inspection is crucial. PAQi’s vision system ensures accuracy through:
High-Resolution Imaging to detect micro-cracks, welding inconsistencies, or coating flaws across the entire part surface.
Automated Defect Detection Models that are custom-trained to identify specific defect types unique to treated metals, like scale formation and tempering cracks.
Traceability and Data Reporting, enabling manufacturers to track inspection results for compliance and continuous improvement.

Precision Measurement for Consistent Quality
For metal parts manufacturers, consistency in dimensions and tolerances is paramount. Any deviation in geometry can impact the performance and safety of parts used in heavy-duty applications. PAQi's measurement capabilities include:
Real-Time Dimensional Verification for features like hole diameters, edge alignment, and thickness.
Automated Calibration Checks that maintain accuracy across shifts, minimizing the need for manual measurements and ensuring parts remain within specification.
Detailed Reporting and Compliance tracking for quality assurance, providing full transparency across all measurements.
Optimized Pick and Place for Manufacturing Efficiency
Handling heavy, heat-treated metal parts requires precision and reliability. Automated pick and place systems powered by PAQi’s AI capabilities are designed to improve handling accuracy and safety by:
Identifying Correct Pick Points based on precise coordinates from image capture.
Integrating with Robotic Systems to automate loading, unloading, and assembly operations without operator intervention.
Minimizing Handling Errors by using real-time vision feedback to adjust the pick and place process, ensuring each part is positioned accurately.
Unique to LM3 Technologies, PAQi’s pick and place solutions come with the benefit of no recurring subscription fees, providing substantial cost savings over time compared to other suppliers.
Precision Torch Cutting for Complex Metal Fabrications
Torch cutting for complex shapes and wear-resistant components requires high precision and adaptability to ensure parts are cut according to exact specifications. PAQi’s vision system assists torch cutting operations by:
Locating Key Reference Points on parts, like holes, edges, and datum points, to calculate accurate cutting paths.
Ensuring Cutting Accuracy within Tolerance, using AI-driven models to maintain alignment with programmed cut paths and prevent material waste.
Streamlining Setup and Calibration to accommodate multiple part types, making it easy for operators to switch between jobs with minimal adjustments.
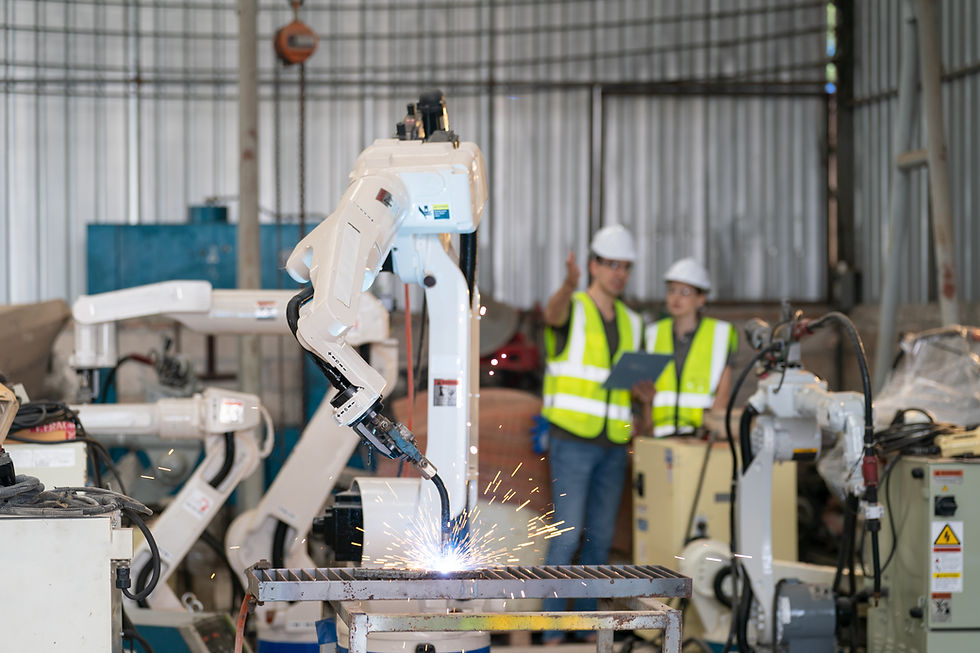
Benefits of AI-Enhanced Automation for Metal Manufacturing
Switching to automated, AI-driven solutions with LM3 Technologies’ PAQi platform provides metal manufacturers with:
Improved Production Throughput: Automated inspection, measurement, and handling reduce bottlenecks and speed up production cycles.
Enhanced Quality Control: High-accuracy inspection and measurement prevent defective parts from reaching end users, preserving product integrity and brand reputation.
Reduced Scrap and Rework: Accurate measurement and cutting ensure each component meets requirements the first time, minimizing waste.
Increased Operator Safety: Automated pick and place systems reduce the need for manual handling of heavy or heat-treated parts, lowering the risk of injury.
Scalability Across Part Types: PAQi’s flexible models allow for seamless adaptation across various parts, reducing setup time and increasing productivity.
Lower Total Cost of Ownership: With no recurring subscription fees, LM3 Technologies provides a cost-effective solution that reduces operational expenses over the product’s lifecycle.
Conclusion
AI-enhanced solutions are transforming metal manufacturing by optimizing precision, efficiency, and safety. LM3 Technologies’ PAQi platform offers comprehensive support for inspection, measurement, pick and place, and torch cutting operations. With a commitment to quality, advanced AI capabilities, and a cost-effective model free from subscription fees, LM3 ensures that metal parts manufacturers can meet the highest standards of production while maintaining efficiency and controlling costs.
Comments